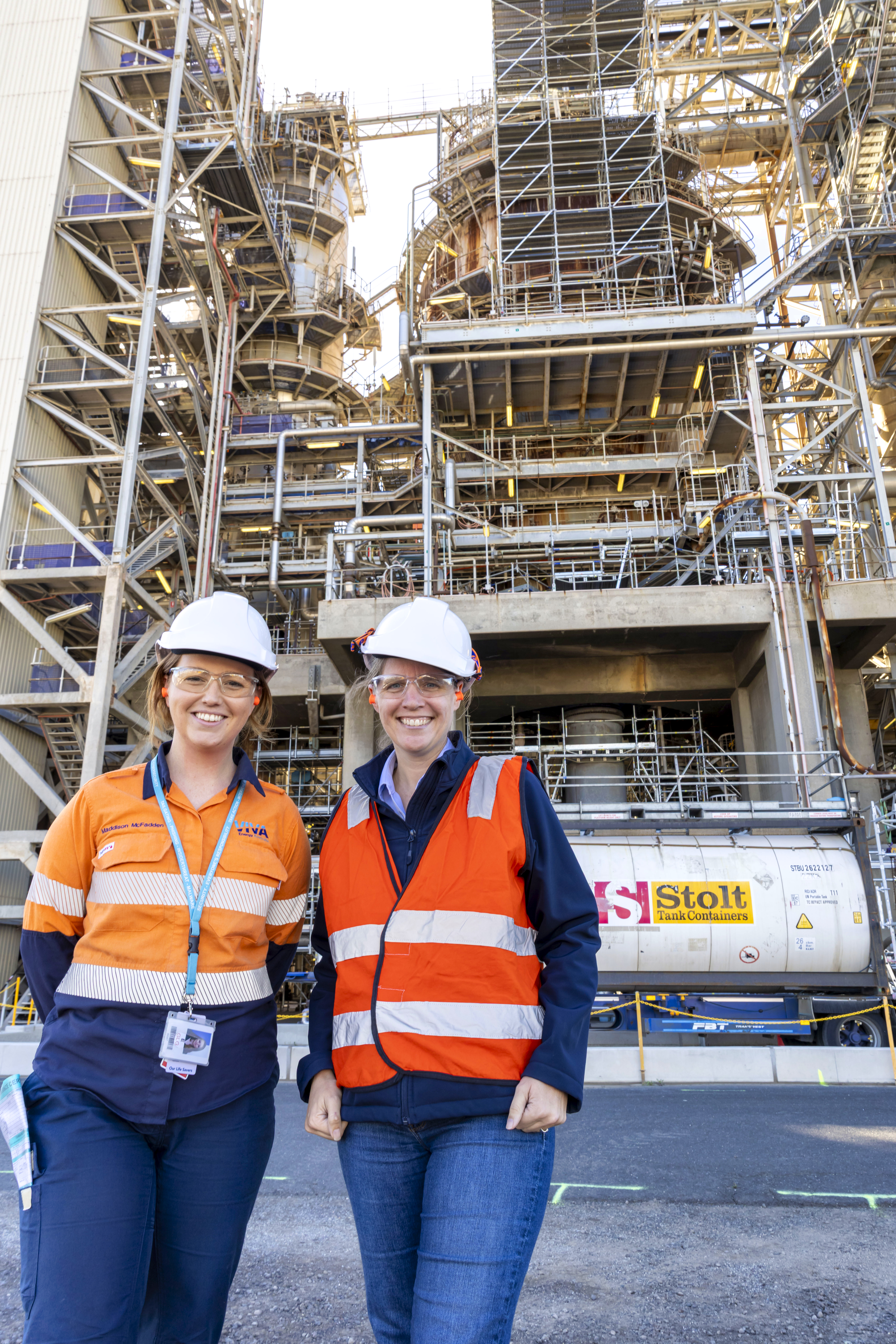
Viva Energy is delighted to announce that this week it successfully processed more than 9.5 tonnes of plastic pyrolysis oil (PPO) at its refinery in Geelong, demonstrating the suitability of the facility for establishing a large-scale waste plastic facility in Australia.
This is a major step forward in Viva Energy’s plans to establish a waste plastic recycling facility with Cleanaway, which – with its national collection and processing footprint – has been exploring options for collecting and sorting used plastic.
This week’s trial proved Viva Energy has the capability to process large volumes of PPO – a critical step in the establishment of a national solution for Australia’s waste plastic problem.
While Viva Energy has processed small volumes of PPO in the past, this volume allowed testing of both the Geelong Refinery infrastructure capability and downstream product-quality impacts. The PPO processed in Geelong was made from waste plastic in Akron, Ohio, in the USA, by Alterra, a leading developer of plastic recycling technology. Viva Energy obtained approval to import this quantity PPO to allow the demonstration to proceed, reflecting the sort of PPO volumes that will be produced from the future Advanced Recycling project.
The focus of the trial was on whether contaminants would impact either the design of the joint venture facility or the ability of the Geelong Refinery to process PPO volumes at scale. The learnings from this trial will be used to inform new packaging design standards to maximise the volumes of soft plastics that can be be processed through advanced recycling technologies.
Viva Energy and Cleanaway are continuing a full feasibility study into the plastic recycling project, with the Front-End Engineering and Design (FEED) phase expected to start in 2026 once details of the Australian Government’s packaging reform have been finalised.
Bill Patterson, Viva Energy’s Executive General Manager – Refining, said it was exciting to see a new future emerge for the refinery. “Over many decades our facility has played an important role in preserving our sovereign manufacturing capability and keeping the country moving,” Mr Patterson said. “We will continue to manufacture the fuels essential for our standard of living, but we will now play an additional critical role establishing a circular economy and helping to address Australia’s waste plastic issue.”
Valerio Coppini, Alterra’s Chief Commercial Officer said Alterra’s thermochemical liquefaction process technology would be critical in efforts to renew discarded plastic back into its original building blocks.
"The Alterra technology has proven the ability to add value to end-of-life, post-consumer plastics by successfully converting them into feedstock for chemicals and new plastic production,” Mr Coppini said. “Following the successful trial at the Geelong Refinery we are looking forward to growing together with Viva Energy and Cleanaway in Australia to divert discarded plastics from landfill, displace virgin, fossil-derived material, and reduce GHG emissions.”
Media Enquiries:
Michael Cave
T: +61 409 647 910
E: [email protected]
About Viva Energy
Viva Energy (ASX: VEA) is a leading convenience retailer, commercial services and energy infrastructure business, with a history spanning more than 120 years in Australia. The Group operates a convenience and fuel network of almost 900 stores across Australia and supplies fuels and lubricants to a total network of nearly 1,500 service stations.
Viva Energy owns and operates the strategically located Geelong Refinery in Victoria, and operates bulk fuels, aviation, bitumen, marine, chemicals, polymers and lubricants businesses supported by more than 20 terminals and about 80 airports and airfields across the country. www.vivaenergy.com.au
About Alterra
Alterra is the developer, operator, and licensor of its thermochemical liquefaction process technology that renews discarded plastic back into its original building blocks, thus minimizing reliance on new, fossil-derived feedstock for the manufacturing of new plastic products. Our commercially operational plastics circularity facility in Akron, OH leverages our unique fully continuous technology to process post-consumer plastic content on a daily basis. By deploying our technology we are Solving Plastic Pollution® through Infinitely Renewed Plastics™.