If you want your business – and your equipment – to run like a well-oiled machine, you need to make the most of your lubricants. Here, Viva Energy Australia’s National Technical Manager Darren Barwick shares his insights on optimising your lubrication.
The performance requirements for lubricants in the mining industry have increased dramatically due to the demands of longer oil drains, higher operating temperatures, increased pressures and loads, and smaller reservoirs.
What’s more, expectations of increased reliability, which is critical to production, are higher than ever. “There’s an old saying that a lubricant is the ‘lifeblood of the machine’,” says Darren. “This couldn’t be more true given the demanding nature of today’s applications.”
It’s vital, then, to optimise lubrication. “The impact of choosing substandard lubrication will be dramatic,” Darren says. “And you’ll see it immediately with component failures, or longer term with reduced reliability, reduced production rates and increased equipment ownership costs.”
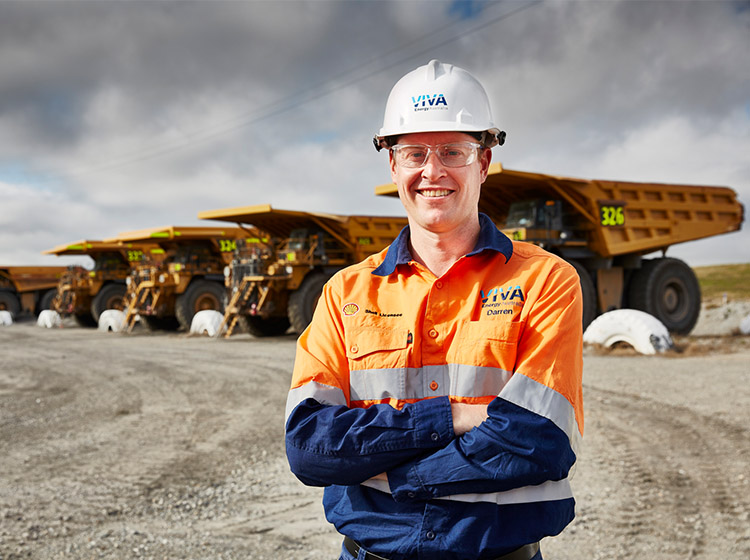
Minimum threshold for machinery requirements
Equipment manufacturers and industry bodies issue lubricant specifications for each component of a machine. “Experience shows us, however, that in today’s mining applications, these specifications represent the bare minimum performance requirements that a lubricant needs to meet,” says Darren. “Typically, satisfying the maintenance regimens of mining operations requires higher levels of performance.”
As mining operations look to reduce costs and complexity by, for example, extending oil drain intervals and through product rationalisation, lubricant performance requirements well exceed these minimum specifications. “Only with extensive lubricant and equipment knowledge, combined with proven field performance, can a technician confidently recommend and optimise lubricants in these applications,” says Darren.
Increasing equipment productivity with synthetics
Extending oil drain intervals depends on several factors – application, loads, contamination, ambient temperatures, utilisation and more. “Even accounting for all of these influences, moving from a mineral oil to a synthetic option typically results in at least double the oil drain interval,” says Darren. “Combine this with the additional operational benefits that synthetics generate, such as improved reliability and energy efficiency, reduced component wear, reduced operating temperatures, wider temperature applications and rationalisation opportunities, and you can see significant justification for using synthetic oils or greases.”
So, is the mining sector widely using synthetic oils? “As technology in both equipment and lubricants improves, the trend in mining is towards higher-performance oils and greases, including synthetics,” says Darren. In the near future, he says, technical advancements in lubricants will see synthetics applied in mobile-plant driveline lubrication, resulting in longer oil drains, better energy efficiency and extended component life.
Safeguarding your equipment’s wellbeing
When you invest in high-quality lubricants, one of the keys to maximising your investment, says Darren, is to keep them clean. Lubricant contamination has a detrimental effect on component life, and it’s all too common for poor maintenance practices and lubricant handling techniques to introduce contaminants on-site. “However, typically, you don’t need large capital investment in infrastructure to improve in this area,” he says. “Rather, a change in culture – through training, focus and ownership – can deliver significant results.”
The future of lubricants
Darren foresees an increase in the use of synthetics in the next five years due to the increased demands on lubricants and the uptake of emerging technologies. However, in the near term, he asserts that mining operations will continue to use a mix of high-quality mineral oils and synthetics. “Most mineral oils used in mining will be Group II – highly refined – products that will replace conventional group I mineral oils,” he says. “Although they don’t deliver the same performance as synthetic products, Group II mineral oils demonstrate improved performance over traditional Group I mineral oils, particularly in oxidation stability and volatility.”
If you’re not getting the most out of your lubricants, it’s time. From their many benefits and ability to meet ever-increasing demands to their promising prospects with a spotlight on synthetics, optimised lubricants are more invaluable than ever to the mining industry.
Need lubricants technical support? Please contact the Viva Energy technical helpdesk on 1300 134 205