Securing the future with co-processing trials
Viva Energy is actively trialling innovative co-processing solutions at its Geelong Refinery. It's the first step in establishing a large-scale chemical recycling facility to reduce plastic waste and extend material life.
The refinery's capability to reprocess waste streams and create new materials – and support the growing demand for recycled content in packaging – is being tested through co-processing trials using existing infrastructure.
One such trial is proving the potential of used cooking oil (UCO) as a lower carbon feedstock. In partnership with Snackbrands Australia and Cleanaway, Viva Energy has trialled transforming UCO into food-grade plastic. It’s a trial that could open future pathways for soft plastic solutions at scale.
An engineer’s guide to transforming UCO into food-grade plastic
Stephanie Backman, Senior Business Development Engineer, and Maddison McFadden, Senior Process Engineer & Future Fuels Lead at Viva Energy, shared an insider’s look at co-processing UCO into snack packaging.
Step by step from cooking chips to new plastic packaging.
It starts with feedstock: used cooking oil
Most food producers use vegetable oil, primarily composed of triglycerides. Over time, the triglyceride molecules break down and oxidise, and the oil is replaced. The waste UCO is then typically used for agricultural feed or sent offshore for diesel production. This is where Viva Energy could offer an alternative solution for the UCO.
“We want to ensure minimal impact to our critically important equipment,” said Stephanie.
“There are precise specifications on what the equipment at our refinery can manage – we don’t want solids, too much water, or acidic water.”
Processing for transport
Scanline, owned by Cleanaway, acts as an aggregator and quality assurance intermediary by collecting, combining and then heating the UCO in the truck at a temperature of over 200 degrees Celsius to separate the oil from contaminants and water.
The clean UCO is transferred to a pressure vessel isotainer which keeps the oil secure as it’s transported to the Geelong Refinery.
At the refinery
On arrival at the refinery, the UCO is weighed and tested to ensure it meets specifications. Then it is injected into the Residue Catalytic Cracking Unit (RCCU), also known as ‘the cracker’, where it helps displace some of the traditional hydrocarbon feeds. The cracker processes the usual crude oil, plus a portion of UCO as an alternate feedstock.
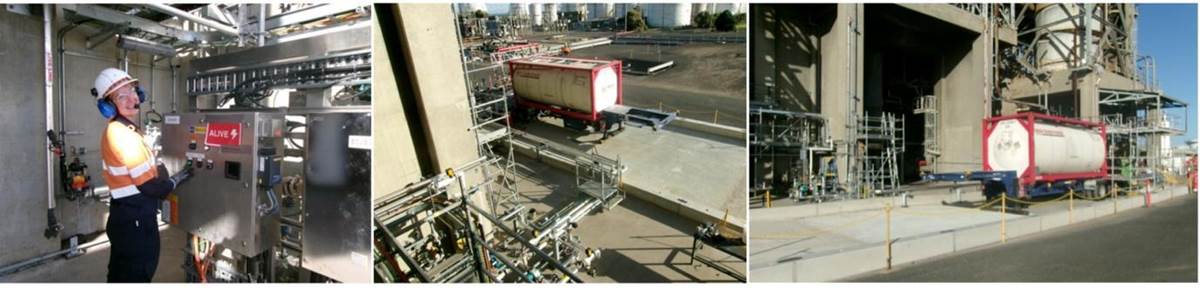
An isotainer of UCO arrives at the Geelong Refinery for co-processing.
The UCO is heated before being injected into the cracker, which breaks down the long-chain molecules into a range of smaller molecules. These smaller molecules are building blocks that can be separated into usable products or reacted to form virgin polypropylene (plastic). To create the finished plastic, the molecules pass through about 10-15 distillation columns, pumps, heat exchangers and reactors.
Transfer to the plastics plant
The propylene is transferred to Viva Energy’s plastics plant, where it is polymerised to make polypropylene. Extruders then form the polypropylene into resin particles.
“The resins are then transported to an external packaging manufacturer and melted down to become bio-circular, food-safe packaging,” said Stephanie.
“In this case, they start another life as chip packets for Snackbrands Australia.”
Traditional vs chemical recycling
Traditional mechanical recycling physically re-granulates plastics to produce secondary raw materials. However, this process uses chemical recycling, resulting in a final product chemically identical to virgin materials.
As Maddison explains: “By introducing a feedstock upstream, whether that’s UCO or recycled plastic, we're able to produce a bio-derived polymer suitable for food grade plastics.”
“That’s important to our customers and only chemical recycling can do that – and our Geelong refinery and polypropylene plant are the last facilities left in Australia with that capability.”
|
The critical equipment making it happen
As the owner and operator of Australia's only plastic resin manufacturing plant, Viva Energy is uniquely placed to provide locally sourced, recycled polymers for sustainable soft plastics.
The cracker is a key part of Viva Energy’s infrastructure with significant scaling capability, enabling the potential to process significant volumes of alternative feedstocks for polymer production.
“The Geelong Refinery already has the processing equipment that would cost billions of dollars to build new,” said Stephanie.
“There are some international refineries processing cooking oil, but this trial is currently the only one in Australia converting it to plastic. It’s what sets this project apart and means we can make a dent in solving these issues.”
Viva Energy is certified under the International Sustainability and Carbon Certification (ISCC+) scheme, which provides customer transparency on the renewable feedstock content of fuels and resins produced. Using the mass balance approach with free attribution ensures an accurate reflection of recycled or bio-based content in the final product.
Read how ISCC+ certification builds credibility at How the Geelong Refinery is developing unique soft plastic solutions
What’s next: Hard-to-recycle soft plastics and used tyres
Leveraging this technology for food packaging is just the beginning; the trial also serves as research and development for larger ambitions involving waste soft plastics recycling and used tyres.
“It’s been a learning exercise to see how UCO can be recycled and how to leverage our existing equipment and processes,” said Stephanie.
Viva Energy is also partnering with Cleanaway on a joint-venture project to produce pyrolysis oil from hard-to-recycle soft plastics. Engineering and design are expected to begin in 2026, pending finalisation of the Australian Government's packaging reforms.
“We believe we can process up to 100,000 tonnes of recycled soft plastic each year, which is close to 20% of Australia’s soft plastic waste. It would be hard to find another trial project coming close to that scale,” said Maddison.
Used tyres are also in Viva Energy’s sights.
“The cracker enables us to scale. We’re expecting that we can add up to 10% of alternate feedstock with oils made from waste tyres and plastics,” said Stephanie.
The refinery team of more than 200 skilled engineers have upskilled to meet the challenge of co-processing and move closer to offering circular and lower carbon solutions.
“Our team understands the role we have to play in the transition to cleaner and lower carbon products,” said Maddison.
“For every truck of UCO we process, we know it’s creating millions of new chip packets. Those numbers have a real impact on motivating the team.”
Stephanie said people are key to the long-term strategic vision for the Geelong refinery as part of the Viva Energy Hub.
“We have the know-how and a very specialised workforce. The Geelong Refinery is uniquely placed to provide important solutions to deliver a circular economy.”
This trial has solidified Viva Energy’s vital role in Australia’s energy future and circular economy. It underscores the support required from government, stakeholders, the community, and customers to make this vision a reality.
Viva Energy – keeping Australians moving today as we build a sustainable future for tomorrow.
Read more about Polymers