When you’re operating in a highly regulated and hazardous environment, there’s no room for error, safe operations and adhering to the regulations is critical. But that doesn’t mean sticking with the status quo.
We look at the ways we’re harnessing innovation and technology in our tank maintenance to improve safety – and prolong the life of our assets. There are risks involved with storing fuels but with good management and safety procedures in place these risks can be managed.
Our Reliability and Integrity team are responsible for managing our assets including tanks, pipelines, electrical and instrumentation, pumps, fire systems and piping.
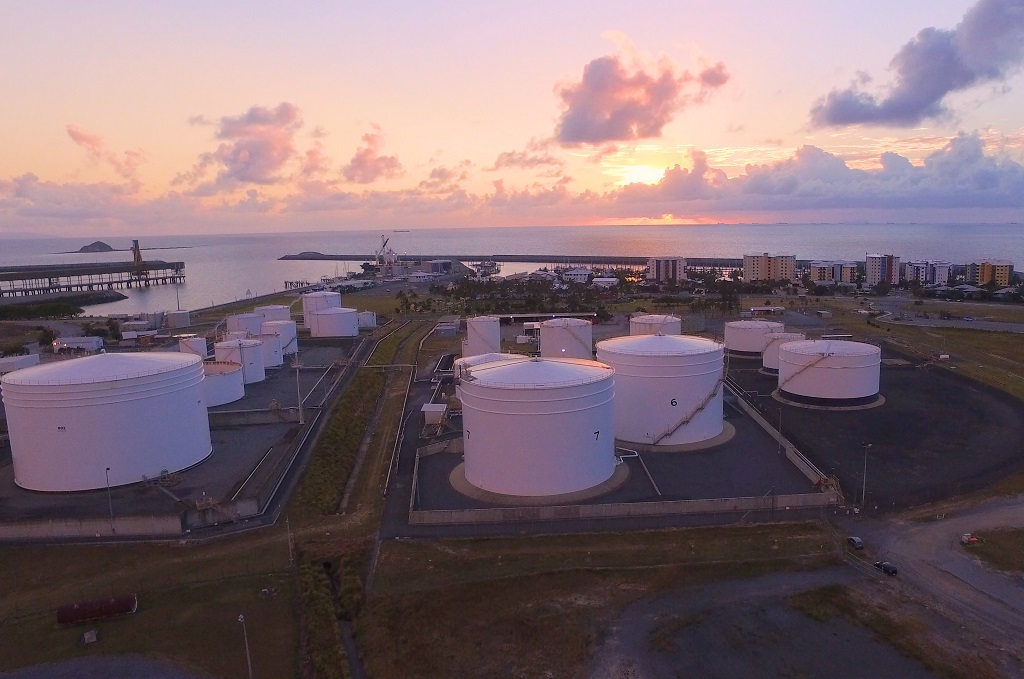
They are at the frontline of our commitment to ensuring that we meet all required regulations and that safe work practices are adhered to at all our facilities from terminals in Devonport and Cairns to pipelines in Sydney.
All tanks great and small
We operate and maintain more than 3000 storage tanks across Australia, including the new 100ML crude oil tank in Geelong – the biggest in Australia. This mega tank measures 21 metres high and a staggering 84 metres in diameter.
From steel and stainless steel vertical tanks carrying a range of petroleum products to fiberglass and steel underground tanks at retail service stations, the range of sizes and models of tanks is impressive and requires detailed management.
We also manage customer tanks at a number of mining facilities across Western Australia and Queensland.
Best practice is the new standard
Tank integrity is paramount to safely storing fuel. But no matter where the tank is, storing fuel is a hazardous operation, and strict regulations require thorough inspection and maintenance programs every step of the way.
For vertical storage tanks, underfloor corrosion of the tank floor is the main threat of potential leaks and to prevent corrosion requires preventing water getting under the tank floor. To reduce the risk of corrosion in our vertical storage tanks, a new best practice process in sealing the tank foundation plinth has been developed. The ‘weather strip design’ – designed by Engineering Services Manager, Tony Toko - prevents water ingress and has been proven to reduce the underfloor corrosion rate, which increases the life of the tank and the length of the service intervals.
“This design is now used for all of our new tank builds within Viva Energy and has even been adopted by other companies in the industry,” Tony says.
Innovate to stay still
While building new tanks is one way to ensure best practice, what do you do when a large proportion of your infrastructure are established assets? For us, it means adopting innovative measures to guard against corrosion, prolonging the lifespan of our tanks, regular inspections and maintenance and ensuring they’re compliant with rigorous regulations and safety standards.
A strict maintenance regime is crucial. “We’ve come a long way in tank integrity in the last 10 years,” says Tony. “We’re happy with the standards of our inspections, the scope of work and specifications, the contractors we use and the quality of repair.” It’s all about having the right processes in place, the right inspection tools and importantly, the right people.
Operators working at our terminals are a key part of the front line of tank maintenance and best practice. Being at the coal face, the operators work every day in and around our assets which means they get to know the assets and, in partnership with the site engineer, they ensure the safe operation of the tanks.
Highlighting our long-term commitment to best practice, 10 years ago we partnered with a local inspection company to bring the first SLOFEC Floor Scanner to Australia from Germany. This high-resolution scanner can differentiate corrosion on the top side of the tank floor versus the underside of the tank floor.
Thanks to the high-resolution data and the ability to detect issues if they are occurring, the SLOFEC has helped us extend our tank maintenance period from the typical seven-to-eight-year to an impressive 15-year interval, taking into account the age of the asset.
In addition, a Risk Based Inspection (RBI) tool developed in-house is used to determine the next maintenance period. “It’s enabled us to have more confidence in how our tanks are behaving as it uses a range of data to understand the risks the tanks are exposed to within the environment they are in and safeguards the tanks integrity. This is a preferable approach compared to one purely based on the age of the tank and the time since the last maintenance event. Having access to this information means that we can assess and consider the maintenance requirements of each individual tank as we now know what is going on inside the tank before we open it up. So rather than taking an approach where we automatically schedule the maintenance over a predetermined time period, we can tailor the maintenance schedule which can result in the tank being maintained more or less frequently.” says Tony.
Tough maintenance regime
But innovative technology is just one part of the puzzle. A rigorous maintenance regime which adheres to the various regulations, has thorough written processes and procedures, uses qualified inspectors and has good communications between staff is all essential to keeping such a large pool of assets maintained. ”On average we spend 21,600 man-hours conducting maintenance turnarounds on around 15 of our tanks each year.”
“When we work on the tanks, we make sure we reinforce the safety messages, that hazards are identified, people are aware of what’s happening in their day, and the controls are in place 100% of the time,” says Tony.
“It is high-risk work,” he explains. “Incidents can happen, especially when there is a change from what was originally planned.”
Whether that change is due to using different tools, a different scope of work, new staff or a change in the weather, it’s vitally important to “recognise the change, then stop work, take five, and review hazards and controls before we restart and complete the job,” he says.
All on the same page
Good relations with our contractors is also vital to ensure compliance, stresses Tony. “Their values have to be our values. Your safety messages have to be their safety messages,” he says. “Then you’re operating on the same wavelength and working towards the same goals.”
It’s the same when dealing with customers. Jeremy Teo, Product Support Engineer at Viva Energy, who offers on-site assistance to help our customers comply with the AS1940 standard and state regulations in relation to tank inspections and maintenance.
“We help our customers identify for their storage tanks where they have gaps from the Australian and industry standards, and help them to close those gaps so they can have peace of mind and reduce their risk profile from an operational and regulatory perspective,” he says.
But, as Jeremy explains, compliance offers benefits apart from improving risk profiles. “Having well maintained tanks and good storage practices means you can maintain the quality and cleanliness of the fuel,” he says. “Good product quality means you’ll have fewer equipment breakdowns, less operational downtime, longer equipment life and reduced maintenance costs.”
Which means it’s great for business too.
To learn more about tank compliance email [email protected]