There is potential to extend the lifespan of your equipment well beyond the manufacturer's recommendations by following these handy maintenance and lubrication tips from Rob Cavicchiolo, Viva Energy Australia's Technical Hub Manager.
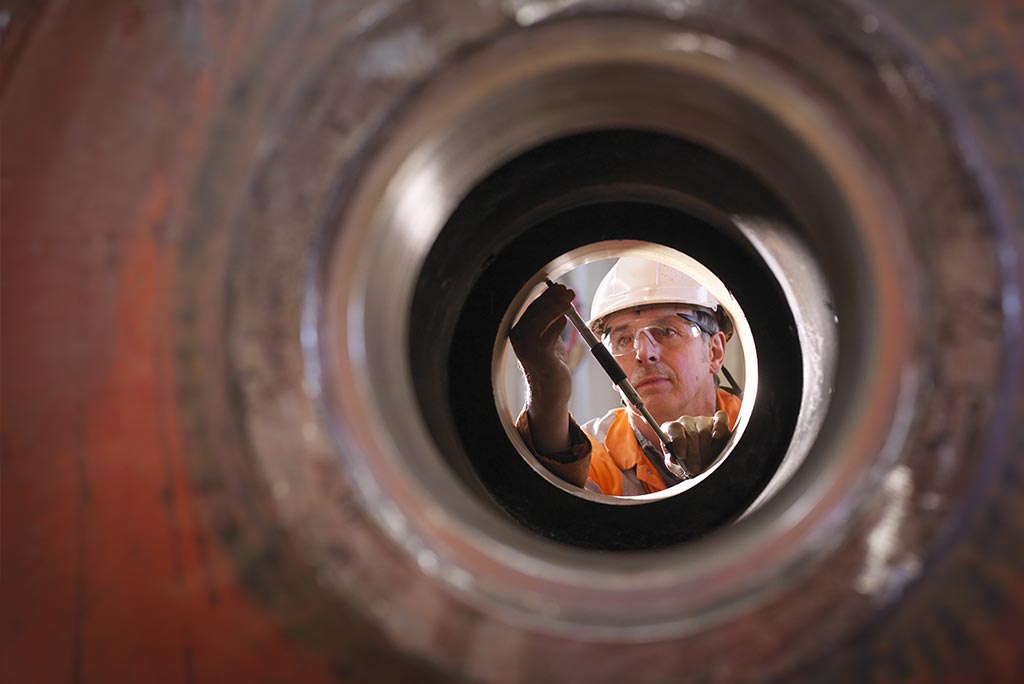
Know your equipment
Currently, across the mining, transport, power, manufacturing and other industries, there’s a tendency to put pressure on assets. The aim of this is to make productivity, efficiency, labour and equipment longevity gains. The problem is, this places stress on equipment componentry, which needs to perform continuously, meaning less time offline for servicing and maintenance.
If you want to push out equipment life beyond its natural lifespan, it's important to make sure you know the manufacturer’s recommendations; their instructions with regard to lubrication requirements, including oil drain intervals (ODIs); and what you need to consider if you want to push your equipment harder.
It’s possible to push out ODIs well beyond the manufacturer’s recommendations − an engine with an ODI of 250 hours can do 500 hours between oil changes. However, you first need expert advice on the appropriate lubricants and services you'll require to do this.
If you ensure you have the right practices in place, that you're using the correct lubricant for the equipment and that you're using appropriate services such as oil analysis, your equipment has the capacity to continue beyond its operational limit and, importantly, to operate efficiently and productively.
Don’t wait until it’s too late
Be aware of signs of equipment wear and tear and other indicators that suggest there is an issue. If equipment isn’t operated or lubricated correctly to meet manufacturer recommendations and suit environmental conditions, it has the potential to suffer from premature failure.
Things like misapplication or cross-contamination of lubricants can play into this, and change the performance and protection offered by lubricants in your equipment – in other words, affect the typical characteristics you need in a lubricant for that application. If this happens, it's important to conduct lubricant testing and seek advice from lubricant specialists who can provide direction on your particular oil issue and the specific equipment it relates to.
Regular servicing, testing and advice is crucial, as is understanding which test is appropriate when conducting oil analysis for a particular type of equipment. For example, tests for a gearbox or diesel engine oil will be completely different from those for turbine oil. Viva Energy provides expert advice about testing suites and test frequency, and employs lubrication specialists to help clients interpret the data on their oil to help build a picture of what's happening with their equipment.
Have a good relationship with your supplier
A good relationship with your lubricant supplier can make all the difference, not only in terms of your equipment lifespan, but also fuel efficiency, equipment up-time and productivity.
Laboratory-level lubricant analysis can indicate whether the lubricant you’re using in machinery is ready to be drained and replaced, or whether it contains contaminants such as silicon or dirt.
More ominously, traces of wear metals might indicate that a serious malfunction is about to occur. It’s important to schedule regular check-ups with lubricant engineers and experts who can advise on a solution that protects your equipment. If your supplier provides this as a holistic service, even better.
Consider changing from mineral to synthetic lubricant
Synthetics are changing the way companies are lubricating their equipment and offer many benefits over traditional oils. Synthetic oils have inherently different properties to mineral oil. For example, they have a higher viscosity index; that is, they have the ability to resist changes in viscosity across different ranges of temperature (low and high temperatures) and can help protect your equipment in demanding conditions.
Additional benefits include a greater resistance to oxidation, and thermal stability, resulting in increased wear protection and long oil life.
There are many reasons to choose a synthetic lubricant over its mineral counterpart. Obviously, requirements will vary from sector to sector, and there may be cost pressures involved with moving to synthetic, but these pressures can be offset by performance improvements and cost savings between oil changes.
Ongoing support from lubricant specialists, correct maintenance programs and regular oil testing can help you to get the most out of your equipment and see productivity and efficiency gains. If you're after technical support, please feel free to contact our technical helpdesk on 1300 134 205 or
Email us here