The Queensland-based Pinkenba bulk lubricants terminal recently converted extensive areas of lighting to LED, due largely to the initiative of one keen-eyed engineer. Ravi Kolli, Maintenance Analyst at Viva Energy Australia, talks about how the energy-efficiency project was managed.
“Viva Energy’s Distribution Manager Vince Neville, asked for ideas that could provide the business with new opportunities for growth or improvement," Ravi says. “Being an engineer with a passion for sustainability, I responded by submitting an idea to upgrade the existing high-intensity lighting at the facility to LED.”
As the proposal was in line with Viva Energy’s ongoing commitment to health, safety, security and environment (HSSE), it was given the go-ahead.
The Pinkenba facility has 284 high-intensity discharge lamps of various types (street, flood and canopy) with wattage ranging from 250W to 1000W. The average life span of these bulbs is two to 2.5 years with the replacement cost of each bulb being between $700-$900. It takes a minimum of two people with an Elevating Work Platform (EWP) and a Working at Heights permit to replace them and they generate 448 metric tons of greenhouse gas emissions yearly.
Existing lighting data was gathered by identifying the type, wattage and location of each light. Light levels were measured to determine the illuminance and uniformity compliance to Australian standards. At the same time, data was collected from electricity bills and maintenance records for the previous two years.
The information was analysed to determine the cause of the intermittent light failures to lessen the cost of light replacements. Results showed annual maintenance costs of around $90,000 and an opportunity to reduce greenhouse gas emissions to 153 metric tons per year.
Following consultation with Maintenance and Projects teams, the lights replacement plan was implemented with the support of senior management at Viva Energy. Old fixtures and mercury bulbs were recycled using a government-certified recycler. Following installation, surveys and measurements were taken to ensure quality and standards were upheld, lighting specifications were updated and electricity bills monitored to realise energy savings.
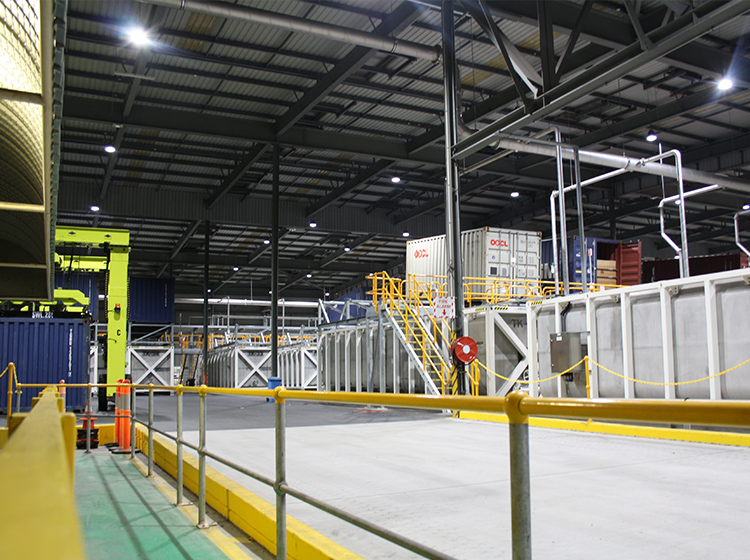
The results are impressive
The newly-installed LED lights resulted in:
- Energy savings of 66 per cent.
- A reduction of 295 metric tons of greenhouse gas emissions per year.
- Elimination of 75 per cent of high-risk work (working at heights) related to light changes by increasing the life of the lights from 2.5 to 10 years.
- Ongoing financial savings of $165,000 per year.
One lesson Ravi learnt was that small changes can make a huge difference.
“Typically, these are just running costs to a big company,” he says. “We have lights, we pay the bill. There was no way of knowing how much wattage or energy we were consuming, or even what lights we had.” The project enabled Viva Energy to measure the data and deliver significant energy and financial savings.
Ravi appreciates that he was given responsibility for the project, and that initiative is encouraged within Viva Energy. “Nevertheless, while we can come up with plans, we have to work collaboratively to get a good positive outcome.
“There’s a lot of opportunity to make a difference at Viva Energy. I simply recognised the issue, developed the business case and implemented it; that is part of our Viva Energy values.”